Bozeman Public Safety Center
Client
Thinkone Architects, City of Bozeman
Location
Bozeman, MT
Industry
Primary Service
Secondary Services
Earthwork Design and Inspection, Foundations, Seismic Site Classification, Ground Improvement, Lab Testing
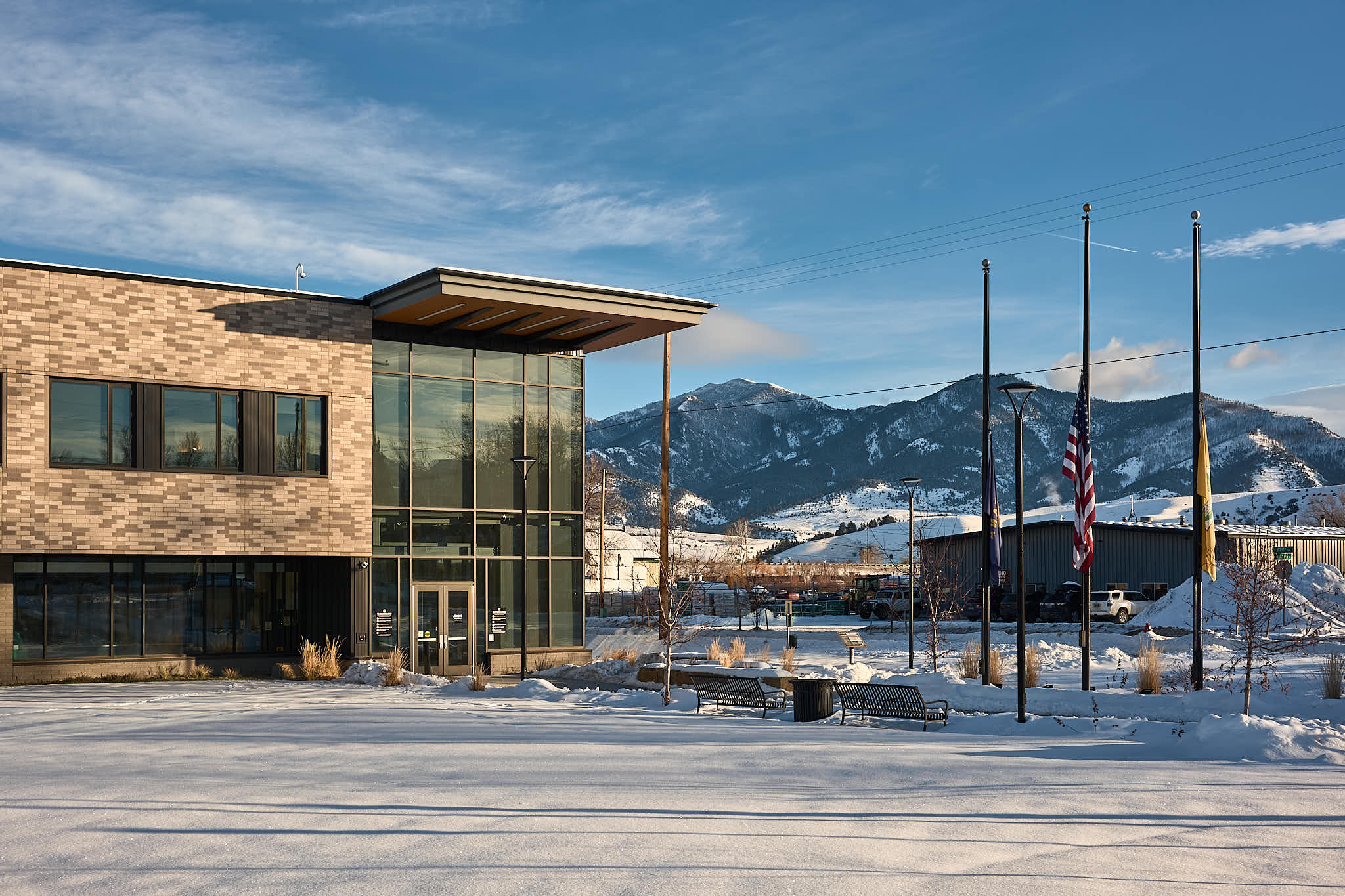
Project Description
The new Bozeman Public Safety Center has been constructed at the site of the former MDT yard facility, located on the southwest corner of N. Rouse Avenue and W. Oak Street on the northeast side of Bozeman. This 8-acre site development includes a large, multi-story building and several asphalt parking lots and roadways. The building houses the police department, the municipal court facilities, and one of the City’s fire stations.
AESI first became involved with the project in 2014 during the initial concept phase. At that time, we were retained for a preliminary geotechnical investigation and report of the subject property. In 2019, as the project design progressed, we performed additional field explorations to better characterize the site conditions. This was followed by the preparation of the final geotechnical report for design and construction.
The two biggest findings of the geotechnical work were that the site was blanketed by a 1.5 to 2.0-foot layer of asphalt millings/roadmix gravel and that the “target” bearing material for the building was the native sandy gravel at a depth of generally 5.0 to 7.0 feet. To save a substantial amount of money, we recommended stripping/salvaging all of the existing asphalt-laden gravel materials from the surface of the site and re-using these materials as part of the sub-base gravel section under new asphalt areas. This saved on both the haul-off of the material and the importing of all new gravel. Due to the footprint size of the building and the number of interior footings, we recognized that traditional footing over-excavation/replacement down to the “target” native gravel would be impractical and uneconomical. Instead of standard foundation earthwork, we recommended a ground improvement system consisting of rammed aggregate piers under all foundation elements (including perimeter, interior, and exterior footings). This foundation system was chosen and designed to include over 650, 30-inch piers that extended down into the “target” native gravel.
AESI has been involved with the site and foundation construction since it began in the spring of 2020. We observed the stripping/salvaging of the asphalt-laden gravel materials, the preparation of subgrade, and the placement of the sub-base gravel sections under new asphalt areas. In the building area, we monitored the construction of the gravel building pad, provided QA inspection/oversight during the installation of the rammed aggregate piers, and observed the foundation excavation and the exposed tops of the piers under footing locations.
Challenges
Site Conditions: The site was covered by a 1.5 to 2.0-foot layer of asphalt millings/roadmix gravel, which required careful management to reuse these materials effectively and economically.
Foundation Design: The native sandy gravel, identified as the “target” bearing material, was located at a depth of 5.0 to 7.0 feet. Traditional footing over-excavation and replacement were impractical and uneconomical due to the building’s footprint and the number of interior footings.
Ground Improvement: Implementing a ground improvement system with over 650 rammed aggregate piers was a significant undertaking. This required precise installation and quality assurance to ensure the stability and integrity of the foundation.
Material Management: Stripping and salvaging the existing asphalt-laden gravel materials and reusing them as part of the sub-base gravel section under new asphalt areas required meticulous planning and execution to save costs and reduce waste.
Coordination and Oversight: Continuous involvement from AESI for site and foundation construction, including monitoring subgrade preparation, gravel building pad construction, and the installation of rammed aggregate piers, was essential to address any issues promptly and maintain project timelines.
Solutions and Results
Reuse of Existing Materials: Stripped and salvaged the existing asphalt-laden gravel materials from the site and reused them as part of the sub-base gravel section under new asphalt areas. This approach saved on both the cost of hauling off the material and the expense of importing new gravel, making the project more economical.
Ground Improvement System: Instead of traditional footing over-excavation, a ground improvement system using rammed aggregate piers was implemented under all foundation elements. This method provided a stable foundation for the building, with over 650, 30-inch piers extending into the native sandy gravel, ensuring the structural integrity of the building.
Cost Savings: The reuse of existing materials and the innovative foundation solution significantly reduced project costs.
Structural Integrity: The ground improvement system ensured a stable and durable foundation, capable of supporting the large, multi-story building.
Efficient Project Execution: Continuous monitoring and quality assurance helped maintain project timelines and addressed any issues promptly, leading to a smooth construction process.