Sullivan Bridge
Client
USFS Regional Geotechnical Services
Location
Flathead National Forest, Flathead County, MT
Industry
Primary Service
Secondary Services
Earthwork Design and Inspection, Seismic Stability, Slope Stability, Foundations, Hydrogeologic Analysis, Lab Testing, Survey (Drone Survey, Bathymetric Survey, Topographic Survey)
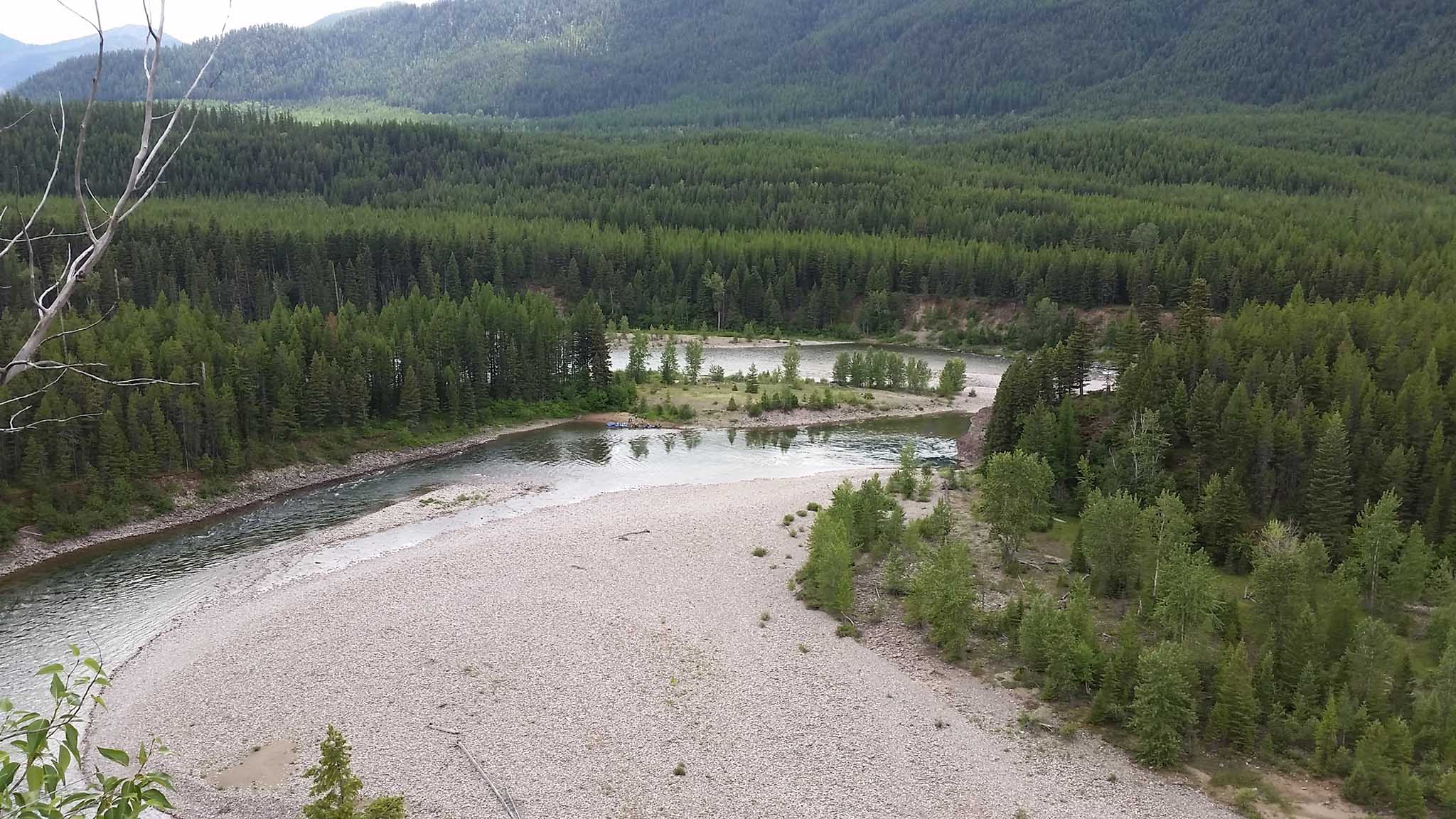
Project Description
As part of their IDIQ contract with the USFS Region One, Allied Engineering provided engineering and surveying services for the repair of the Sullivan Bridge gabion abutment on the north side of the east abutment of the bridge.
Sullivan Bridge is located on National Forest System Road 895 in a remote area on Hungry Horse Reservoir. An initial site visit was conducted in July 2016 by Allied Engineering and the US Forest Service. Following the field visit, it was decided that the failing gabions should be removed, the slope re-shaped and protected to minimize erosion and channelization, and an engineered toe should be built and backfilled with riprap up to the existing road shoulder. All survey, evaluation, and construction needed to consider steep slopes and cliffs inaccessible to most equipment.
The site was surveyed with a combination of high-definition scanning, bathymetric surveys with GPS integrated depth finder, and conventional survey and GPS. Several different design and construction options including barge access, long reach excavators, and specialty drilling and anchoring equipment, and techniques were then considered and discussed by Allied Engineering and the Forest Service. The preferred alternative included removing the existing gabion baskets entirely and replacing them with a stacked riprap fill slope. Because the catch point is a thin section of steep bedrock, the toe of the riprap is supported by gabion reno mattresses anchored into the rock with driven rebar pins. These pins and mattresses help to buttress the bottom of the riprap slope along with providing some vertical clearance between the bottom of the rock and the existing bedrock catch point. Construction documents were developed in September 2016 including plans, engineer’s opinion of probable construction cost, supplemental specifications, and schedule of items. A report was also prepared to summarize the design process and describe how and why the final design was chosen.
Challenges
Remote Location Access: Sullivan Bridge is located in a remote area on Hungry Horse Reservoir, making access challenging. Transporting personnel, equipment, and materials to such an isolated site would require careful logistical planning, potentially increasing costs and project duration.
Steep Slopes and Inaccessible Terrain: The project area included steep slopes and cliffs that were largely inaccessible to standard construction equipment. Working on these slopes required specialized surveying and construction techniques and equipment, adding complexity to the planning and execution.
Erosion and Slope Stability: The site’s steep and unstable slopes posed a risk of erosion and channelization, particularly after removing the failing gabions. The team had to carefully re-shape and reinforce the slope to prevent future erosion and maintain long-term stability, which required precise engineering and innovative solutions.
Technical Survey Requirements: The combination of high-definition scanning, bathymetric surveys, GPS, and conventional survey techniques presented technical challenges. Integrating and analyzing data from different survey methods required advanced expertise and coordination to ensure accuracy.
Limited Equipment Options: Due to the site’s inaccessibility, traditional construction equipment was unsuitable. The team had to consider alternative approaches, such as barge access, long-reach excavators, and specialty drilling and anchoring equipment, requiring significant planning and potentially high equipment rental costs.
Anchoring in Bedrock: The design required that the toe of the riprap slope be anchored into steep bedrock using gabion reno mattresses and rebar pins. Anchoring into thin, steep bedrock presents challenges with securing materials effectively, requiring precise drilling and reinforcement to ensure stability.
Environmental Protection: Working near a reservoir necessitated additional precautions to protect water quality and surrounding habitats. Implementing these environmental safeguards while conducting construction on steep and fragile slopes would add another layer of complexity to the project.
Design Complexity and Safety: The unique challenges of the site required careful design considerations and coordination between Allied Engineering and the US Forest Service. Safety for workers on steep slopes, handling heavy materials, and dealing with specialized anchoring and drilling techniques added risk that required stringent safety protocols and oversight.
Development of Comprehensive Construction Documents: Given the site’s complexities and remote nature, developing thorough construction documents, specifications, cost estimates, and schedules would be essential to mitigate the high risks and unpredictability associated with this project.
Solutions and Results
Comprehensive Site Surveying: Allied Engineering used a combination of high-definition scanning, bathymetric surveys with GPS-integrated depth finders, and conventional surveying methods to accurately map the complex terrain. This multifaceted approach ensured precise data collection, which was essential for creating a tailored engineering solution.
Specialized Equipment for Inaccessible Terrain: The project team considered various options to overcome the remote, steep terrain, including barge access and long-reach excavators. Ultimately, they opted for specialty drilling and anchoring equipment that allowed work on steep slopes and difficult-to-reach areas, improving safety and effectiveness in the challenging environment.
Re-shaping and Stabilizing the Slope: To address erosion and slope instability, Allied Engineering reshaped the slope and protected it with an engineered toe structure backfilled with riprap. This reinforced slope reduced erosion risk and prevented future channelization, providing long-term stability for the bridge’s foundation.
Anchoring with Gabion Reno Mattresses and Rebar Pins: The design called for removing the failing gabions and constructing a stacked riprap slope, reinforced at the base with gabion reno mattresses. These mattresses were anchored into the steep bedrock using driven rebar pins, which provided a stable foundation and prevented slope movement along the bedrock’s edge.
Collaborative Design Process: Allied Engineering worked closely with the US Forest Service to explore various design options, ensuring the chosen solution met safety, budgetary, and environmental considerations. This collaborative approach allowed the team to select the best possible alternative given the project’s unique constraints.
Improved Structural Stability: The re-shaped slope with stacked riprap and anchored gabion mattresses provided a stable, resilient foundation for the bridge, protecting it from erosion and future deterioration.
Extended Service Life of the Bridge: The reinforced abutment and stable slope foundation significantly enhanced the longevity of Sullivan Bridge, ensuring it can withstand environmental pressures and serve the public for years to come.
Enhanced Safety and Accessibility: By stabilizing the slope and creating a secure foundation, the project improved the overall safety and accessibility of National Forest System Road 895, benefitting those who rely on this remote route.
Environmental Protection: The engineered slope and riprap design minimized erosion and preserved the surrounding natural landscape, helping to protect the reservoir and local ecosystem from sedimentation and potential contamination.